The Essential Guide to Building Production Rates from Scratch
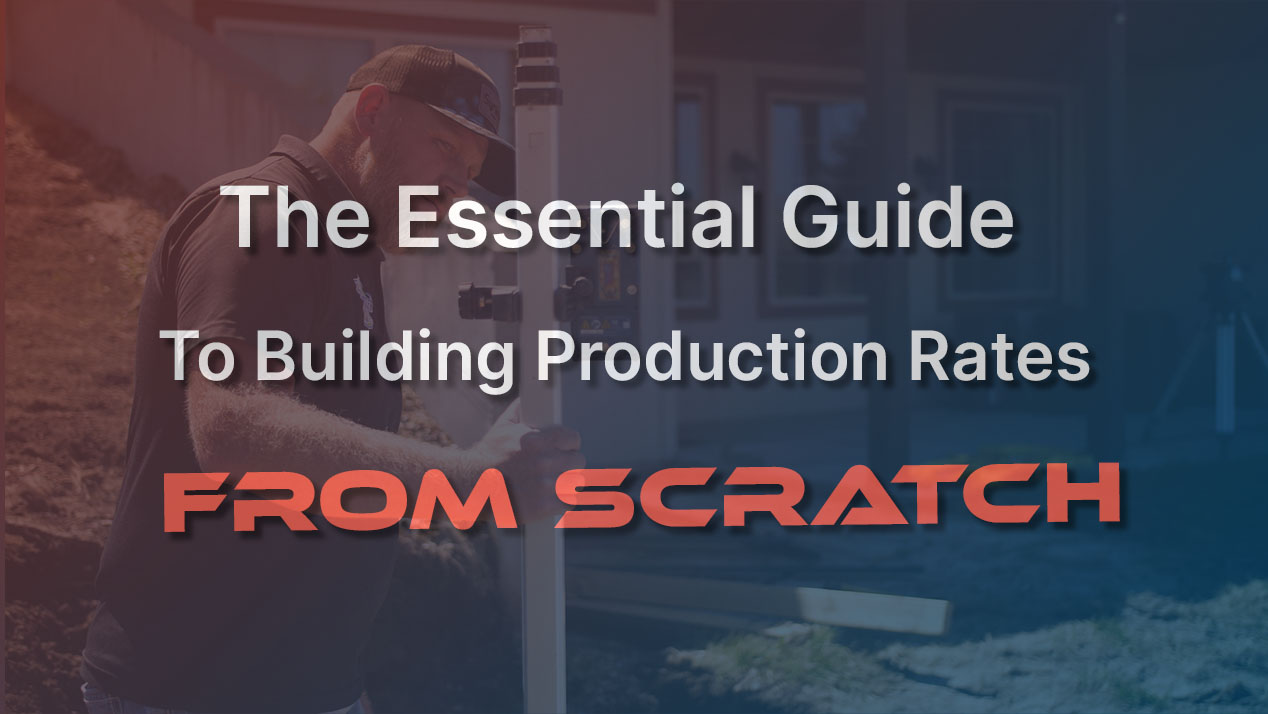
Are there industry standard production rates?
Well… no. There may be an industry average production rate, but not an industry standard.
I get questions all the time “Hey, I want to start using production rates, what’s an industry standard that I can use?”
Using an industry-standard seems logical, but it isn’t. It’s a little like, say, you are building a vehicle, and you want to know what the industry average is on fuel mileage. There is an industry average, yes, but depending on what vehicle you are building, you could be way lower or way higher than that average.
The same is true for production rates.
How do you start using production rates?
The answer to that question lies with you. I’m going to cover how to build production rates that you can use, rely on, and are based on your production ability, not someone else’s.
Things that can and do impact your production rate:
- equipment
- crew experience
- job site access
- installation methods
and more, all have an impact on your production rate.
If you’re starting from ground zero, here’s how I’d go about it:
- Look at the last 3-6 (or more) jobs you did, and find two numbers for each job: How many manhours it took, and how many units (ie sq ft).
- Then, take the units (ie sq ft) divided by man hours it took for each job.
- Lastly, average the job’s results (the more jobs, the more accurate).
The key to getting this info is having easy and ready access to those two numbers for each job:
- how long it took
- how many units
This starts by tracking time, aka your entire company clocking in on the SynkedUP app.
If you don’t do this, you’ll never get the data you need to find your production rates. And of course, it’s usually pretty easy to get the units in retrospect. You usually know how many lineal ft, sq ft, etc. something was, or at least can go measure.
Here’s a simple example
Patio Job 1 – 85 manhours / 250 sq ft patio = 2.94 sq ft per manhour.
Patio Job 2 – 250 manhours / 1150 sq ft patio = 4.6 sq ft per manhour.
Patio Job 3 – 135 manhours / 525 sq ft patio = 3.88 sq ft per manhour.
2.94, 4.6, 3.88 averaged out is 3.8 sq ft of patio installed from start to finish per manhour.
The more jobs you track, the more accurate your production rate is.
Once you establish and get comfortable with your own production rate, I’d recommend evolving up to have 3 different production rates: easy access, medium access, and difficult access production rates, as you begin tracking more and more jobs.
This will allow you to look at a job you are bidding, determine that this is a “difficult access” job, and then you use your difficult access production rate. Allows you to get more nuanced and accurate according to site conditions.
So, the sad reality is, no, you can’t use someone else’s production rates. You can look at them to determine where you are in relation to an average if you want, out of pure interest’s sake. But certainly do not base a real quote on them.
You want your quotes to be based on your numbers (your own budget and overhead) and your own production rates. Anything else is playing Russian roulette with your profits.
Keep in mind, once you did the initial work and built your first iteration production rates, don’t slack off. You can never stop tracking. Even your own production rates evolve over time, as you gain experience, try new products, get new equipment, etc
In Conclusion
So to sum it all up, if you are at ground zero, and have literally nothing to go on, start tracking time on each job. No need to overcomplicate it and track every single task, like excavating, compacting, laying pavers, cutting, etc. Just track the job from the time you pull out of the shop until the last truck comes back after the job is done. I’m a fan of KISS. Keep It Simple Stupid. There’s always time to get more nuanced and categorized later. Start in baby steps, and just get a simple production rate to start. From the time you start the job, til you wrap up. Then divide the units by the man hours, and you have your benchmark.
If you want to upgrade your own systems and processes, and want to start leveraging the power of production rates, track time, and job cost each job, we’ve got software tailor-made to do this. If you want to learn more about it, hit me up on Instagram @synkedup or book a demo here, and we’ll show it to you on screen share and answer your questions.
If you already are using SynkedUP, and want a hand in building a production rate, hit us up on the chat in the lower right corner of our website, and we’ll give you a hand. Or you can check out a tutorial I made here, with a production rate calculator spreadsheet.
Cheers!
Enjoy the New Years’ weekend!
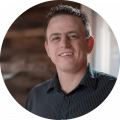
Weston Zimmerman
CEO and co-founder
See SynkedUP in action
Related Articles
Choosing a Landscape CRM: The Features Every Contractor Needs
Crews keep calling? They may not be a people problem; it might be your process. Here's how to fix it...
How do you get your crews to perform like all stars?
Crews keep calling? They may not be a people problem; it might be your process. Here's how to fix it...
How To: Win More Jobs Without Marketing More
Want to win more jobs without spending more on marketing? The secret is in your old proposals. Here's how to...
The Power of Habit in Growing Your Business
Are your habits moving your business forward, or quietly holding you back? Small actions repeated daily are what really drives...
The Cost of: Scattered Focus
Cutting costs isn't the same as saving money. Learn how to use leverage, not panic, to drive real profit and...
Onsite vs. Offsite Time n Your Jobsites
On-site vs off-site crew time impacts more than productivity; it hits your profits. Learn to cut waste and boost margins...
Tips To: Improve Client Experience
Your sales process might not be broken; it might be overcomplicated. Here are 5 simple ways to improve client experience,...
What is the Most Difficult Challenge You’ve Overcome?
Business is tough. Growth is tougher. But if you're still standing, you're stronger than you think. Here's a reminder from...
Why Time Tracking is Critical for Contractors
This new time tracking update helps you spot labor overruns in real time, so you stop the bleeding before it's...
Why Cutting Costs Isn’t the Same as Saving Money
Cutting costs isn't the same as saving money. Learn how to use leverage, not panic, to drive real profit and...